ریخته گری تحت فشار یا دایکاست چیست؟
ریخته گری تحت فشار یا دایکاست، یکی از متداولترین روشهای تولید انبوه قطعات فلزی غیر آهنی کوچک تا متوسط با استفاده قالبهای دائمی است. این روش، کاربرد بسیار گستردهای در ساخت قطعات مورد استفاده در صنعت اتومبیلسازی دارد. اغلب قطعات دایکاست از جنس آلومینیوم هستند. ریختهگری تحت فشار، امکان ساخت قطعات فلزی ساده تا پیچیده با ساختار یکپارچه را فراهم میکند.
دنده شانه ای چیست؟
کاربرد دایکاست چیست؟
حدود ۶۰ درصد از قطعات ساخته شده به روش ریختهگری تحت فشار در صنعت خودروسازی مورد استفاده قرار میگیرند. البته این روش ساخت و تولید در صنایع هوافضا، تجهیزات الکترونیکی، لوازم خانگی و جواهرسازی نیز به کار برده میشود.
دنده مدول چیست؟
دایکاست چگونه اجرا میشود؟
دایکاست طی پنج مرحله شامل آمادهسازی قالب، تزریق مواد مذاب، خنککاری، باز کردن قالب و برشکاری انجام میگیرد. فرآیند اجرای ریختهگری تحت فشار، شباهت بسیار زیادی به قالب گیری تزریقی (ساخت قطعات یکپارچه پلاستیکی) دارد.
آشنایی با دنده شانه ای و دنده مدول
مواد قابل استفاده در دایکاست چه هستند؟
بیش از ۸۰ درصد از قطعات دایکاست با استفاده از آلومینیوم و آلیاژهای مختلف آن نظیر زاماک ساخته میشوند. مس، منیزیوم، روی و قلع نیز کاربرد زیادی در فرآیند ریختهگری تحت فشار دارند.
تجهیزات مورد استفاده در دایکاست چه هستند؟
به طور کلی، دو نوع دستگاه شامل دستگاه دایکاست با سیستم تزریق محفظه گرم و دستگاه دایکاست با سیستم تزریق محفظه سرد در ریختهگری تحت فشار مورد استفاده قرار میگیرند.
دستگاههای محفظه گرم در ساخت قطعاتی از جنس روی، قلع و سرب (آلیاژهای دارای نقطه ذوب پایین) و دستگاههای محفظه سرد در ساخت قطعاتی از جنس آلومینیوم، برنج و منیزیوم (مواد دارای نقطه ذوب نسبتا بالا) کاربرد دارند. فشار عملیاتی دستگاههای محفظه گرم (۶۹ تا ۳۴۵ بار)، معمولا پایینتر از فشار عملیاتی دستگاههای محفظه سرد (۱۳۸ تا ۱۳۸۰ بار) است.
قالب دایکاست، از دیگر تجهیزات اصلی در اجرای ریختهگری تحت فشار است. این قالب، از اجزای متعددی تشکیل میشود که بر روی روند ساخت و کیفیت قطعه نهایی تاثیر میگذارند. طراحی قالب دایکاست، از مهمترین مراحل آمادهسازی در تولید قطعات دایکاست به شمار میرود.
انواع دایکاست کدام هستند؟
به طور کلی، ریختهگری تحت فشار بالا، به عنوان روش اصلی و استاندارد دایکاست شناخته میشود. با این وجود، محدودیت به کارگیری مواد در این روش، باعث توسعه فرآیندهای متنوعی از دایکاست شده است. هر یک از این فرآیندها، امکان ساخت قطعات با کیفیت، از جنس فلزات مختلف را فراهم میکنند. از انواع روشهای دایکاست بر اساس مکانیزم اجرا میتوان به موارد زیر اشاره کرد:
ریخته گری تحت فشار بالا: ساخت قطعاتی از جنس آلومینیوم، برنج و منیزیوم (مواد دارای نقطه ذوب نسبتا بالا) توسط دستگاه دایکاست محفظه سرد
ریخته گری تحت فشار پایین: ساخت قطعاتی از جنس روی، قلع و سرب (آلیاژهای دارای نقطه ذوب پایین) توسط دستگاه دایکاست محفظه گرم
ریخته گری تحت فشار در خلا یا ریخته گری تحت خلا: ساخت قطعات نیازمند عملیات حرارتی
ریخته گری تحت فشار کوبشی یا ریخته گری کوبشی: تقویت مواد الیافی و آلومینیوم مذاب
ریخته گری تحت فشار نیمه جامد: ساخت قطعات منیزیمی و آلیاژهای آلومینیومی برای دستیابی به چگالی حداکثری و تخلخل حداقلی
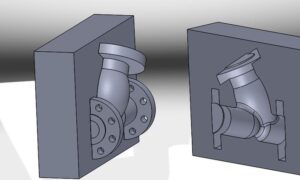
ریخته گری چدن
مزایا و معایب دایکاست چیست؟
ریختهگری به روش دایکاست دارای مزایای متعددی است که مهمترین آنها عبارت هستند از:
راندمان تولید بالا
دقت ساخت خوب در ابعاد قطعات
پرداخت خوب سطح و حجم پایین ماشینکاری مورد نیاز
هزینه عملیاتی پایین در تولید انبوه
هزینه پایین نیروی کار
یکپارچگی بالای قطعه
مقاومت بسیار مناسب در برابر خوردگی
از محدودیتهای اصلی دایکاست میتوان به موارد زیر اشاره کرد:
مناسب نبودن برای فلزات و آلیاژهای دارای نقطه ذوب بالا مانند فولاد
محدودیت ساخت قطعات بزرگ یا دارای طول بلند
هزینه بالای سرمایهگذاری و تهیه قالب
طولانی بودن فاصله زمانی بین دریافت سفارش تا تحویل کامل قطعات
عدم صرفه اقتصادی برای تولید قطعات در تعداد کم
امکان تشکیل حباب و تخلخل داخل قطعه
نظری نیست.