اصطلاحات ریخته گری
قالب ریخته گری
«قالب» (Mold یا Mould)، ابزاری است که به منظور شکلدهی به فلز مذاب مورد استفاده قرار میگیرد. قالب ریختهگری تحت فشار با اصطلاح «دای» (Die) شناخته میشود.
طراحی قالب های صنعتی مورد استفاده از فعالیتهای بسیار مهم در فرآیند ریختهگری به شمار میرود؛ چراکه تمامی بخشهای موجود در قالب، بر روی کیفیت قطعه ریخته گری شده تاثیر میگذارند.
حفره قالب
«حفره» (Cavity)، فضای خالی درون قالب و مقصد نهایی مواد مذاب است. مواد مذاب با پر کردن حفره قالب، ساختار کلی قطعه مورد نظر را تشکیل میدهند.
سیستم راهگاهی قالب
«سیستم راهگاهی» (Gating system)، مجموعهای از مجراهای درون قالب است که امکان هدایت مواد مذاب از بیرون قالب به درون حفره را فراهم میکند. حوضچه، اسپرو، چشمه، راهبار، تغذیه، راهبار، راهباره و دریچه، از بخشهای اصلی سیستم راهگاهی به شمار میروند.
قطعه ریخته گری شده
قطعه ریخته گری شده، جسمی است که پس از فرآیند انجماد از درون حفره قالب خارج میشود. به قطعه ریخته گری شده، اصطلاحا «کستینگ» (Casting) میگویند.
دنده شانه ای چیست؟
درجه یا فلاسک
دُرجه یا «فلاسک» (Flask)، ابزاری است که به منظور نگهداری قالب ریخته گری مورد استفاده قرار میگیرد. این وسیله، فقط دارای دیوارههای جانبی است و هیچ بخش بالایی یا پایینی ندارد. مقطع فلاسک، معمولا به شکل مقاطع سادهای نظیر مربع، مستطیل و دایره است.
نیمه های فلاسک
اغلب روش های ریخته گری، از قالبهای دو تکه برای ساخت قطعات استفاده میکنند. از اینرو، فلاسک نیز به صورت دو تکه ساخته میشود. به بخش بالایی فلاسک، «کوپ» (Cope) و به بخش پایینی آن، «درگ» (Drag) میگویند.
چیک
در ریختهگریهای پیچیده، فلاسک، از چندین تکه (بیش از دو تکه) تشکیل میشود. به بخشهای میانی فلاسک در این حالت، «چیک» (Cheek) میگویند.
دنده مدول چیست؟
ماسه ریخته گری
ریخته گری ماسه ای به عنوان متداولترین روش اجرای ریختهگری شناخته میشود. ماده اصلی در ساخت قالبهای این فرآیند، ماسه است. فراوانی و هزینه پایین ماسه سیلیسی، این ماده را به گزینه اول ساخت قالبهای ماسهای تبدیل میکند. البته انبساط حرارتی بالای ماسه سیلیسی، احتمال رخ دادن عیوب ریخته گری را افزایش میدهد. ماسه تر یا ماسه سبز، سیلیکات سدیم یا شیشه مایع و ماسه رزینی از رایجترین مواد مورد استفاده برای ساخت قالبهای ریختهگری هستند.
ماسه رزینی
ماسه رزینی، مادهای است که معمولا از ترکیب ماسه سیلیسی ریزدانه با رزین فنولی ترموست تشکیل میشود. مخلوط کردن این مواد با یکدیگر، امکان ساخت قالبهای سخت با استحکام بالا را فراهم میکند.
ماسه رویه
«ماسه رویه» (Facing Sand)، ماسهای است که برای ساخت بخشهای قالب در مجاورت مدل استفاده میشود. ماسه رویه در ارتباط مستقیم با مواد مذاب قرار میگیرد. از اینرو، این ماسه از مقاومت بسیار بالایی در برابر تنشهای حرارتی اعمال شده از طرف مواد مذاب بهره میبرد.
آشنایی با دنده شانه ای و دنده مدول
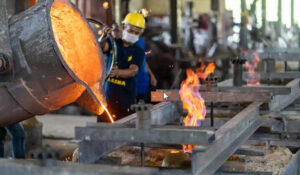
ریخته گری چدن
مدل یا الگو
مدل یا «الگو» (Pattern)، جسمی کاملا مشابه با قطعه نهایی ریخته گری است. این جسم به منظور ایجاد حفره قالب (فضای جریان یافتن مواد مذاب) مورد استفاده قرار میگیرد. از مواد قابل استفاده برای ساخت مدل ریخته گری میتوان به چوب، فلز و پلاستیک اشاره کرد.
مغزه یا ماهیچه
ماهیچه یا «مغزه» (Core)، قطعهای مجزا در قالب ریخته گری است که به منظور ایجاد بازکننده و فضاهای توخالی در قطعه مورد استفاده قرار میگیرد. در صورت پیچیدگی ساختار داخلی قطعه و عدم امکان دستیابی به شکل مورد نظر توسط مدل، از ماهیچه درون حفره قالب استفاده میشود. به این ترتیب، مواد مذاب، محل قرارگیری ماهیچهها را پر نمیکنند. ماهیچهها از ابزارهای پرکاربرد در فرآیندهای ریختهگری به شمار میروند.
چپلت
«چپلت» (Chaplet)، قطعه کوچک فلزی است که به منظور نگهداری ماهیچه در حین فرآیند ریخته گری مورد استفاده قرار میگیرد. چپلتها، از جابجایی ماهیچه بر اثر نیروهای اعمال شده از طرف جریان مواد مذاب جلوگیری میکنند.
چیل
«چیل» (Chill)، قطعهای است که به منظور بهبود فرآیند انجماد (افزایش نرخ خنک شدن)، درون حفره قالب یا اطراف آن جانمایی میشود. در ریختهگریهای پیچیده، عدم تقارن شکل و ضخامت قطعات، از انجماد خطی و یکنواخت بخشهای مختلف جلوگیری میکند. چیلها، با تنظیم انتقال حرارتی در نقاط بحرانی، باعث تعدیل فرآیند انجماد میشوند. جنس این قطعات از مواد دارای هدایت الکتریکی بسیار بالا است.
پاتیل
«پاتیل» (Ladle)، وسیلهای است که منظور انتقال و ریختن ماده مذاب در فرآیند ریخته گری مورد استفاده قرار میگیرد. پاتیلها اغلب در کارخانههای ذوب کاربرد دارند. این وسایل در ابعاد کوچک (با ظرفیت حدود ۲۰ کیلوگرم) و بزرگ (با ظرفیت حدود ۳۳۰ تن) ساخته میشوند. برخلاف بوته، پاتیلهای معمولی درون کوره قرار نمیگیرند. برخی از کورههای پایتلی، از قابلیت اعمال حرارت به فلز و ذوب آن بهره میبرند.
بوته
«بوته» (Crucible)، ظرفی است که به منظور نگهداری فلزات در حین فرآیند ذوب مورد استفاده قرار میگیرد. بوته ریخته گری معمولا از جنس مواد سرامیکی یا فلزی با نقطه ذوب بسیار بالا ساخته میشود. این وسیله درون کوره قرار میگیرد و حرارت کوره را به فلز درون خود انتقال میدهد. پس از ذوب شدن فلز، بوته برای شروع فرآیند ریختهگری به محل قرارگیری قالب انتقال داده میشود.
حوضچه بارریز
«حوضچه بارریز» (Pouring Basin)، یک حفره کوچک قیفی شکل در بخش بالایی قالب است که به منظور ریختن مواد مذاب به درون حفره داخلی استفاده میشود. حوضچه بارریز، نرخ جریان مواد مذاب را تنظیم میکند و اغتشاشات مواد در ورودی راهگاه را کاهش میدهد. تصویر زیر، بیانگر بخشهای مختلف قالب ریختهگری ماسهای و سیستم راهگاهی درون آن است. اصطلاحات مورد استفاده در اغلب روشهای ریختهگری، به یکدیگر شباهت دارند.
اسپرو یا راهگاه بارریز
راهگاه بارریز یا «اسپرو» (Sprue)، مجرای هدایت مواد مذاب از حوضچه بارریز به حفره قالب است. این مجرا، معمولا به شکل مخروطی طراحی و ساخته میشود. در بسیاری از موارد، کنترل جریان مواد مذاب توسط راهگاه بارریز انجام میگیرد.
چشمه راهگاه
در انتهای راهگاه بارریز و در محل اتصال آن با راهبار، فضایی وجود دارد که با تجمع مواد مذاب، از سقوط آزاد آنها جلوگیری میکند. به این فضا، چشمه راهگاه میگویند. چشمه راهگاه، اغتشاشات جریان و گیر کردن هوا درون مواد مذاب را کاهش میدهد. مقطع این چشمه معمولا به شکل دایره، قطر آن حدود دو برابر قطر انتهای راهگاه و عمق آن حدود دو برابر عمق راهبار است.
رانر یا راهبار
راهبار یا «رانر» (Runner)، مجرایی است که مواد مذاب را از راهگاه به دریچه یا تغذیه های اطراف حفره قالب هدایت میکند. رانرها با کاهش سرعت مواد مذاب، باعث جریان یکنواخت آنها به بخشهای مختلف حفره میشوند. این مجراها، معمولا در بخش پایینی قالب قرار دارند.
دریچه یا راهباره
راهباره یا دریچه «Gate یا Ingate»، مجرایی است که مواد مذاب را از راهبار به حفره اصلی قالب هدایت میکند. طراحی راهباره، باعث تغذیه یکنواخت حفره با نرخ ثابت و مطابق با نرخ انجماد میشود. در اغلب موارد، مقداری از مواد مذاب درون دریچه یا حتی دیگر مجراهای سیستم راهگاهی باقی میمانند. این مواد به همراه مواد درون حفره، طی فرآیند انجماد، سخت میشوند. از اینرو، پس از باز کردن قالب و خارج کردن قطعه، نیاز به عملیات ماشینکاری برای تهیه قطعه یا قطعات نهایی خواهد بود.
رایزر یا تغذیه
منبع تغذیه یا «رایزر» (Riser)، فضاهایی درون سیستم راهگاهی قالب هستند که در هنگام توقف ریختن مواد مذاب، به عنوان مخازن ذخیره و تامین مواد مورد استفاده قرار میگیرند. با توقف فرآیند ریختن، مواد مذاب درون حفرهها، بر اثر فرآیند انجماد، شروع به جمع شدن میکنند. کاهش حجم ناشی از جمعشدگی، باعث کاهش ابعاد و تغییر شکل قطعه ریختهگری شده نسبت به قطعه طراحی شده میشود. رایزرها، با تامین مواد مذاب اضافی، تاثیر جمعشدگی بر مشخصات ابعادی قطعه را کاهش میدهند. بر اساس دسترسی یا عدم دسترسی مجرا به بیرون قالب، رایزرها به انواع بالاسری (دسترسی از بالای قالب)، کناری (دسترسی از کنارههای قالب) و کور (بدون دسترسی) تقسیم میشوند.
غلاف رایزر
«غلاف رایزر» (Riser Sleeve)، قطعهای استوانهای شکل است که به منظور کاهش افت حرارتی رایزر توسط ایجاد عایق حرارتی و یا تولید حرارت برای جلوگیری از افت دما مورد استفاده قرار میگیرد. این قطعه، با کاهش میزان جمعشدگی، باعث پیوستگی فرآیند ریختهگری و افزایش کیفیت قطعه نهایی میشود.
هواکش
«هواکش» (Vent)، مجرای کوچکی است که امکان خروج هوا و گازهای ایجاد شده در قالب را فراهم میکند. طراحی مناسب هواکشها، از اهمیت بالایی برای جلوگیری از عیوب ریختهگری مرتبط با حضور گازها برخوردار است. هر چه سطح هواکشها از مقاومت کمتری در برابر جریان هوا برخوردار باشد، خروج گازها با سهولت بیشتری انجام میگیرد.